la fonction d'un responsable de la gestion de stock?
14 h 53
Lorsqu'il travaille en entrepôt, le responsable gestion des stocks
coordonne et planifie l’activité des chefs d’équipe qui eux même
supervisent des manutentionnaires et des caristes. Il suit les
marchandises (produits alimentaires, articles high tech, textile...) de
la réception à la livraison. Dans l’industrie, il gère les stocks de
pièces détachées utiles à la fabrication. Le responsable de gestion des
stocks consacre une grosse partie de son temps à gérer des bases de
données, car tout est informatisé. Sa mission essentielle consiste à
optimiser les flux et les processus. Il veille à la qualité des
marchandises reçues ou à envoyer. Il gère les réclamations, vérifie que
les bons de commande sont aux normes. Quitte à appeler les clients -
distributeurs, chefs de rayon ou de production pour éviter les litiges.
Les journées de travail démarrent parfois à 5 heures du matin pour finir
à 20 heures. La pression des délais est très forte, Son pire cauchemar est
la rupture de stock.
La démarque et sa gestion
12 h 37
COURS
La gestion de la démarque, principale cause de la démotivation du personnel, impose une remise en cause des méthodes de gestion des contrôles, dans tous les flux matières et financiers.
La
démarque est l’obsession de la distribution, qui à cause de son
amplitude peut voir rapidement s’effacer ses bénéfices. La tradition de
la porosité de la caisse rend difficile à contrôler à partir d’un
croisement entre mouvements produits et mouvements financiers, des flux
‘disparus’ ; les contrôleurs fiscaux ne sont pas mieux armés.
La
démarque inconnue ( pertes non enregistrées hors inventaires ) a
beaucoup de sources et représente sur le commerce Français en coût
matière, un montant annuel de 4,35 Milliards d’Euros (1,29% du CA HT contre 1,23 % en moyenne européenne ) . Le Center for Retail Research (2006) donne la répartition suivante :
Donc
la cause est incertaine, le lieu et le moment indéfini et le constat
aléatoire. Cette démarque est mesurée en coût de perte de coût produit,
mais n’inclue pas les coûts de contrôle qui s’élèvent en France à 1,44
Milliards € ( hors coûts traditionnels d’inventaires et coûts de
systèmes d’information ) .
La
gestion de la démarque incombe habituellement au personnel de magasin
qui statistiquement en est une cause pour 1/3 ; il existe alors un
traumatisme certain à faire réaliser un contrôle par une équipe qui
s’auto-soupçonne. Le résultat économique est souvent déplorable, créant
dans les équipes ‘magasins’ des dysfonctionnements préjudiciables à
l’efficacité merchandising.
Le
coût global de la démarque est tellement supérieur, au strict coût de
la perte, que les méthodes de gestion des contrôles si elles aboutissent
à drastiquement limiter la démarque inconnue peuvent présenter, sans
scandale dans la distribution accompagnée, un coût nettement supérieur à
celui de la démarque constatée avec les contrôles traditionnels : ce
coût n’atteindra jamais le cumul des pertes matière avec la charge de
gestion du turn-over ajouté du coût des ventes et clients perdus. Dans
les boutiques d'une enseigne de luxe connue, l'ambiance déplorable créée
par le soupçon et les surcroit d'horaires liés aux pertes et au
tentatives de contrôle, transpire jusque dans les contacts
clients/équipe et provoque méventes et perte de clientèle. 
Les
ventes de produits à forte valeur et à faible volume sont évidemment
les plus surveillées, et celles sur lesquelles les méthodes les plus
avancées sont testées. Pas forcement duplicables, avec d’autres
contraintes de volume ou de prix unitaire, voir de disposition magasin,
les expériences de la gestion de la démarque méritent d’être résumées
ici dans leurs échecs et leurs réussites.
Un
préalable évident : il n’est possible de prêcher la vertu, sans un
minimum d’exemplarité. Le contrôle de la démarque engage l’enseigne et
les points de vente, dans un processus de transparence des flux
matières, financiers, encaissement et de présence de personnel. Il faut
l’accepter. Ainsi dans cette chaine de restauration, toutes les entrées
matière sont pesées et toutes les sorties également par destination y
compris les pertes. La production code barrée est comparée à la commande
et à la consommation qui est mise en regard de l’encaissement. Le
coulage est alors informatiquement contrôlé dans des marges de tolérance
qui permettent l’effort commercial ; et les pratiques d’élasticité
liées à des entrées parallèles sont strictement encadrées. Aucun prélèvement de caisse avec ou sans refonte du ticket Z n'est donc possible.
Toutes
les solutions employées ont pris en compte la globalité de la chaine de
gestion des flux matières et des flux financiers. Sans cette approche
globale, les différentes sources d’erreurs polluent les informations qui
permettent de juguler, correctement les flux jusqu’à l’encaissement
bancaire. Toujours dans l’étude du CRR, l’étiquetage électronique à la
source sur base EAS ( qui permet le contrôle également à la sortie )
représente au mieux 10 % d’une catégorie de produit ( cosmétiques ).
L’étiquetage électronique à la source permet de quantifier des étiquettes attachées à un produit mais n’est efficace dans la suite de sa vie que pour assurer une sécurité de sortie ( vol à l’étalage ). C’est donc vers l’identification unitaire à la source ( électronique type RFID UHF, ou non ) que se sont portées depuis 1996, les expériences des enseignes très soumises aux risques de démarque. Il est intéressant de voir en 2006 quelles sont les attentes de la distribution vis-à-vis de la RFID et de mettre ces attentes en perspective des avantages tirés du retour d'expérience :
L’étiquetage électronique à la source permet de quantifier des étiquettes attachées à un produit mais n’est efficace dans la suite de sa vie que pour assurer une sécurité de sortie ( vol à l’étalage ). C’est donc vers l’identification unitaire à la source ( électronique type RFID UHF, ou non ) que se sont portées depuis 1996, les expériences des enseignes très soumises aux risques de démarque. Il est intéressant de voir en 2006 quelles sont les attentes de la distribution vis-à-vis de la RFID et de mettre ces attentes en perspective des avantages tirés du retour d'expérience :
L’identification
unitaire répond au premier item ( Inventaires et distribution ) avec
pertinence. Inventorier par comptage d’unités est beaucoup moins aisé
que d’accumuler des unités différentes : l’absence de risques de
doublons ouvre l’inventaire dans l’espace et dans le temps ; il permet
sur des sites multiples de gérer ‘’l’absent’’ sur la durée. Autre
avantage attendu dans ce premier Item, la rapidité liée au transport
électronique de l’information, d’où l’absence de manipulation mais aussi
de visibilité du produit. L’expérience montre que le bât blesse et que
des correctifs sont à apporter. Ce qui est lu c’est
l'identifiant de l’objet et non l’objet lui-même et quand l’objet est un
contenant, l’identifiant du contenant et non le contenu ( voir
le cas Viagra ). Dans un inventaire physique, la quantité est associée
au produit vu. Des mesures ont donc été imaginées pour s’assurer d’un
meilleur taux de correspondance. Un inventaire en lui-même ne corrigera
pas la démarque, il sert à évaluer et qualifier un stock. Croisé
avec le contrôle des flux d’entrée et de sortie, l’inventaire offre une
représentation de la démarque potentielle, depuis le dernier
inventaire, à un instant et pourrait participer à la prévention des
pertes ( 2em Item ).
Cette
étude ( CRR ) montre encore combien la démarche du contrôle de la
démarque subit encore l’influence exclusive du vol à l’étalage et des
coûts directs de personnel. C'est-à-dire des deux sources majoritaires
de coûts. Et ce même dans des secteurs ( distribution parfum/cosmétique )
ou de par les dires des logisticiens, la démarque et le coulage ont
lieu tout au long de la chaîne et ou l’ambiance de l’accompagnement est
prépondérante pour la vente et la conservation du client.
Les
entreprises qui ont accepté, très tôt d’évoluer dans cette démarche,
ont rapidement compris que la démarche était globale ou qu’elle n’était
pas. Par exemple les flux de facturation ne sont plus liés au flux
théoriques d’expédition, mais aux flux constatés d’articles/objets mis
dans leur contenant d’expédition lui même scellé et identifié.
Pour
que le contrôle des flux d’articles, soit peu couteux et surtout peu
traumatisant pour les équipes, il est inclus dans l’amélioration de la
gestion administrative et technique des flux y apportant des services
complémentaires ( ex : la traçabilité et la garantie fraicheur).
L’efficacité du système impose que sans unité de lieu et de temps, et
comme l’erreur est intrinsèque à chaque processus humain, la traçabilité
de tous les passages serve de base au contrôle effectif des démarques
inconnues.
Les
flux financiers sont ensuite raccordés aux flux d’articles et ce
exhaustivement pour que la balance flux financiers, flux matière soit
intégralement équilibrée, jusqu'aux contrôles bancaires. Il est donc
nécessaire qu’en l’absence d’EAS chez certains fournisseurs, un organe
de répartition vienne apposer les identifiants et que soient créés des
objets services pour toutes les ventes non associées à des mouvements
d’articles.
La
sortie magasin est contrôlée grâce à la disposition des traceurs et des
portiques qui s’inscrivent dans la dynamique de liberté du chaland (
découverte , appropriation, déambulation ), et sont incorporés au
concept. La trace de sortie d’objets non passés en caisse semble être en
voie de résolution avec des RFID puissantes. Tout en étant conscient
que la désolidarisation du traceur et de son support reste la faille
essentielle de ces sécurités aveugles.
L’inventaire
et l’implication du personnel magasin devient une formalité dans un
océan d’informations qui recoupées permettent d’encadrer la probabilité
de la source de la démarque. La méthode de gestion de stock Wilson
18 h 19
COURS
Issue de la recherche opérationnelle, la formule de Wilson (1934) ou formule du lot économique détermine la période optimale de réapprovisionnement d'une unité de production (magasin, usine). Elle est couramment employée par les services logistiques. Elle a en fait été introduite dès 1913 par Harris.
Elle se fonde sur un modèle simpliste optimisant le coût de gestion d'un stock dans le cadre d'une période fixe de réapprovisionnement


Le coût de gestion est évalué comme la somme d'un coût de stockage et d'un coût de lancement. Le coût de stockage est supposé linéaire en le nombre moyen d'unités en stock. Comme à chaque début de période on commande exactement les unités pour la consommation de la période, le stock initial est






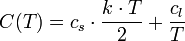


En effet, les coûts de stockage sont en partie non proportionnels à la quantité stockée (c'est le cas par exemple du coût de location du hangar, structure), et les coûts de lancement sont difficile à évaluer : lancer une commande supplémentaire coûte le temps des salariés qui sont rémunérés (charge de travail affectée à une tâche), et quelques frais de papier/téléphone. Il faudra nécessairement prendre en compte les coûts de transport liés à la commande.
Tout savoir sur la Point de Commande
17 h 35
COURS
Le point de commande rythme la gestion des approvisionnements
Outre la méthode du Kanban, du
juste-à-temps et du lean management, la méthode du
point de commande
est appliquée dans le cadre de la gestion des approvisionnements.
Elle implique un
approvisionnement de quantité égale à des dates variables.Point de commande : définition
Tout comme la méthode Kanban, la méthode du point de commande est utilisée dans un système de flux tendus. Elle consiste à définir un stock minimum qui, une fois atteint, déclenche l'approvisionnement : cela permet de réduire le stockage et les coûts associés.Mise en œuvre de la méthode
Calcul du point de commande
La calcul du point de commande implique une parfaite connaissance :- de la consommation ;
- de la production.
(Stock d'origine / Délai de consommation ) x
Délai de livraison
Le délai d'approvisionnement ou de livraison
Le délai d'approvisionnement est un élément clé de la méthode du point de commande. Il doit être connu pour chaque période de l'année et chaque jour de la semaine.Le délai d'approvisionnement inclut :
- le passage de la commande ;
- la réception de la commande par le fournisseur ;
- le traitement de la commande ;
- l'envoi et le transport de la commande ;
- la livraison et la réception de la commande.
En savoir plus : rangement
stockage
Avantages de la méthode du point de commande
La méthode du point de commande est applicable dans toutes les entreprises, mais est souvent privilégiée par celles qui travaillent en flux tendus.La méthode du point de commande possède de nombreux avantages, comme :
- la facilité de gestion grâce aux outils informatiques ;
- l'adaptation automatique en cas d'irrégularité de consommation ;
- la réduction des coûts de stockage ;
- l'absence de sur-stockage.
Inconvénients du point de commande
Elle possède aussi quelques inconvénients :- La gestion des stocks doit être stricte afin de minimiser le risque de rupture.
- Le délai de livraison doit être connu et pris en compte.
- Il faut impérativement créer un stock de sécurité pour assurer la production pendant l'approvisionnement, ou en cas d'augmentation soudaine des ventes.
Mouvements de stock en Gestion des articles
17 h 22
Utilisation
Les coûts réels peuvent être imputés à un support de coûts selon les mouvements de stock suivants :
- sorties de marchandises ;
- entrées de marchandises pour les commandes ;
- entrées de facture pour les commandes.
La sortie de marchandises entraîne les conséquences suivantes dans le système :
- Le stock magasin est diminué de la quantité prélevée.
- La valeur des marchandises sorties est calculée en utilisant la quantité prélevée et le prix dans la vue Comptabilité de la fiche article.
- En Comptabilité financière, l’écriture Compte variation de stock sur compte de stock est passée.
- Le support de coûts est chargé sous une nature comptable primaire.
- Un document article est généré en MM.
- Une pièce comptable est générée en FI.
- Un poste individuel est généré en CO.
Si vous utilisez la composante Achats en Gestion des articles, vous pouvez créer manuellement une demande d'achat pour un support de coûts (comme pour un support de coûts général). La demande d'achat se traduit par une commande envoyée à un fournisseur. À la livraison, l'entrée de marchandises est imputée directement au support de coûts pour lequel l'article a été demandé.
Pour les activités, vous pouvez également créer une demande d'achat. La demande d'achat génère une commande. À la livraison, l'entrée de marchandises est imputée directement au support de coûts pour lequel l’activité a été effectuée.
Pour les articles non gérés en stock et les activités externes, les entrées de marchandises peuvent se produire avant ou après l'entrée de facture :
- Entrée de marchandises avant l'entrée de facture
- Entrée de marchandises après l'entrée de facture
Rangement des Produits
17 h 35
COURS
Aménager le local de stockage et les étagères comme suit:
Dans le cas où l'on utilise des palettes, empiler les cartons sur les palettes -
Pour l'ensemble du stockage:
Dans le cas où l'on utilise des palettes, empiler les cartons sur les palettes -
• à 10 cm (4 pouces) au moins du sol
• à 30 cm (1 pied) au moins des murs et des autres piles
• sur une hauteur ne dépassant pas 2,5 m (8 pieds, règle générale).
• Respecter les instructions du fabricant ou du fournisseur sur la procédure de stockage, ainsi que les conditions d'entreposage figurant sur les étiquettes.
• Placer les produits liquides sur les étagères les plus basses ou en dessous des autres produits.
• Entreposer les produits qui nécessitent d'être conservés au froid dans des zones contrôlées, maintenues à une température appropriée.
• Entreposer les produits à haut risque/de grande valeur dans des zones de sécurité convenables.
• Retirer sans délai les produits endommagés ou périmés du stock utilisable et les éliminer selon les procédures établies (voir la section consacrée à la gestion des déchets).
• Toujours stocker les produits d'une manière qui facilite l'application de la stratégie de gestion de stock «premier périmé, premier sorti.»
• Disposer les cartons de manière à ce que les flèches pointent vers le haut et à ce que les étiquettes d'identification, les dates de péremption et les dates de fabrication soient visibles. En cas d'impossibilité, écrire le nom du produit et sa date de péremption clairement sur la partie visible.
Inventaire Physique
17 h 31
COURS
L'inventaire physique est l'opération consistant à compter
manuellement le nombre des produits de chaque type présents dans le
magasin à un moment donné. L'inventaire physique permet de vérifier que
les soldes de stocks disponibles enregistrés sur les registres
correspondent bien aux quantités de produits réellement disponibles dans
le magasin. Lors d'un inventaire physique, compter chaque produit
individuellement par nom générique, forme galénique et dosage.
Il existe deux types d'inventaires physiques -
L'inventaire physique complet: Tous les produits sont comptés en même temps. Il convient de procéder à un inventaire physique complet au moins une fois par an. Des inventaires plus fréquents (une fois par trimestre ou par mois) sont recommandés. Pour les entrepôts de grandes dimensions, cette opération peut imposer la fermeture pendant une journée ou plus.
L'inventaire physique tournant ou aléatoire: On procède au dénombrement de produits choisis et on vérifie que le résultat concorde avec les registres de tenue de stocks en les comptant à tour de rôle ou régulièrement tout au long de l'année. Cette opération est aussi appelée inventaire tournant.
Il est plus facile d'effectuer régulièrement un inventaire physique complet dans les établissements qui gèrent de faibles quantités de produits. L'inventaire physique tournant convient habituellement aux établissements qui gèrent de grandes quantités de produits.
Un inventaire physique tournant peut être organisé de plusieurs façons -
Par forme galénique: Compter les comprimés en janvier, les gélules en février, les liquides en mars, etc.
Par emplacement dans le local de stockage: Compter les produits se trouvant sur les étagères 1 à 4 en janvier, sur les étagères 5 à 8 en février, etc.
En fonction de la disponibilité du personnel: Compter quelques articles tous les jours, chaque fois que le personnel dispose d'un peu de temps.
Stock disponible: Compter périodiquement chaque article dont le stock disponible se trouve à un niveau inférieur ou égal au stock minimal. Cette méthode peut se révéler plus rapide, dans la mesure où les quantités à compter sont plus faibles.
Dans le cas où l'on fait un inventaire physique tournant, compter
chaque produit au moins une fois au cours de l'année. Compter plus
fréquemment les articles qui partent rapidement et les produits dont le
stock est maximal.
Etapes à respecter dans la réalisation d'un inventaire physique:
1 Plan d'action.
2 Affectation du personnel.
3 Organisation du local de stockage.
4 Dénombrement des produits utilisables.
5 Mise à jour des registres de tenue de stock.
6 Mesures prises suite aux résultats de l'inventaire physique.
7 Discussion des résultats de l'inventaire avec le personnel de l'établissement.
Il existe deux types d'inventaires physiques -
L'inventaire physique complet: Tous les produits sont comptés en même temps. Il convient de procéder à un inventaire physique complet au moins une fois par an. Des inventaires plus fréquents (une fois par trimestre ou par mois) sont recommandés. Pour les entrepôts de grandes dimensions, cette opération peut imposer la fermeture pendant une journée ou plus.
L'inventaire physique tournant ou aléatoire: On procède au dénombrement de produits choisis et on vérifie que le résultat concorde avec les registres de tenue de stocks en les comptant à tour de rôle ou régulièrement tout au long de l'année. Cette opération est aussi appelée inventaire tournant.
Il est plus facile d'effectuer régulièrement un inventaire physique complet dans les établissements qui gèrent de faibles quantités de produits. L'inventaire physique tournant convient habituellement aux établissements qui gèrent de grandes quantités de produits.
Un inventaire physique tournant peut être organisé de plusieurs façons -
Par forme galénique: Compter les comprimés en janvier, les gélules en février, les liquides en mars, etc.
Par emplacement dans le local de stockage: Compter les produits se trouvant sur les étagères 1 à 4 en janvier, sur les étagères 5 à 8 en février, etc.
En fonction de la disponibilité du personnel: Compter quelques articles tous les jours, chaque fois que le personnel dispose d'un peu de temps.
Stock disponible: Compter périodiquement chaque article dont le stock disponible se trouve à un niveau inférieur ou égal au stock minimal. Cette méthode peut se révéler plus rapide, dans la mesure où les quantités à compter sont plus faibles.
Etapes à respecter dans la réalisation d'un inventaire physique:
1 Plan d'action.
• Dans le cas d'un inventaire physique complet, prévoir le (ou les) jour(s) et l'heure.
• Dans le cas d'un inventaire physique tournant ou aléatoire, identifier les produits à compter et la durée nécessaire pour le faire.
2 Affectation du personnel.
3 Organisation du local de stockage.
• Ranger les produits selon la stratégie «premier périmé, premier sorti.»
• S'assurer que les boîtes et les cartons ouverts sont visibles.
• Mettre de côté les produits endommagés ou périmés.
4 Dénombrement des produits utilisables.
• Compter les produits par unités sous lesquelles ils sont délivrés (p. ex. par comprimé ou par pièce) et non par carton ou par boîte.
• Estimer les quantités contenues dans les récipients ouverts pour les produits emballés en vrac. Si une bouteille de 1000 gélules est pleine aux deux tiers, estimer son contenu à 650 ou 700 gélules. Dans le cas d'une bouteille de sirop d'un litre à moitié pleine, estimer son contenu à un demi-litre.
5 Mise à jour des registres de tenue de stock.
• Inscrire la date de l'inventaire physique et les mots Inventaire physique.
• En utilisant une encre de couleur différente, inscrire la quantité de produit obtenue pendant l'inventaire.
6 Mesures prises suite aux résultats de l'inventaire physique.
• Si les résultats de l'inventaire physique diffèrent du solde figurant sur la fiche de stock, mettre à jour ce solde en soustrayant ou en ajoutant les quantités en excès ou manquantes.
• Eliminer les produits endommagés ou périmés trouvés au cours de l'inventaire physique.
• Dans l'un et l'autre cas, identifier, documenter et corriger la cause du problème.
7 Discussion des résultats de l'inventaire avec le personnel de l'établissement.
• Féliciter le personnel, s'il y a lieu.
• Prendre des mesures correctives si nécessaire.
S'abonner à :
Messages (Atom)